Cannabis companies are overlooking this key to success
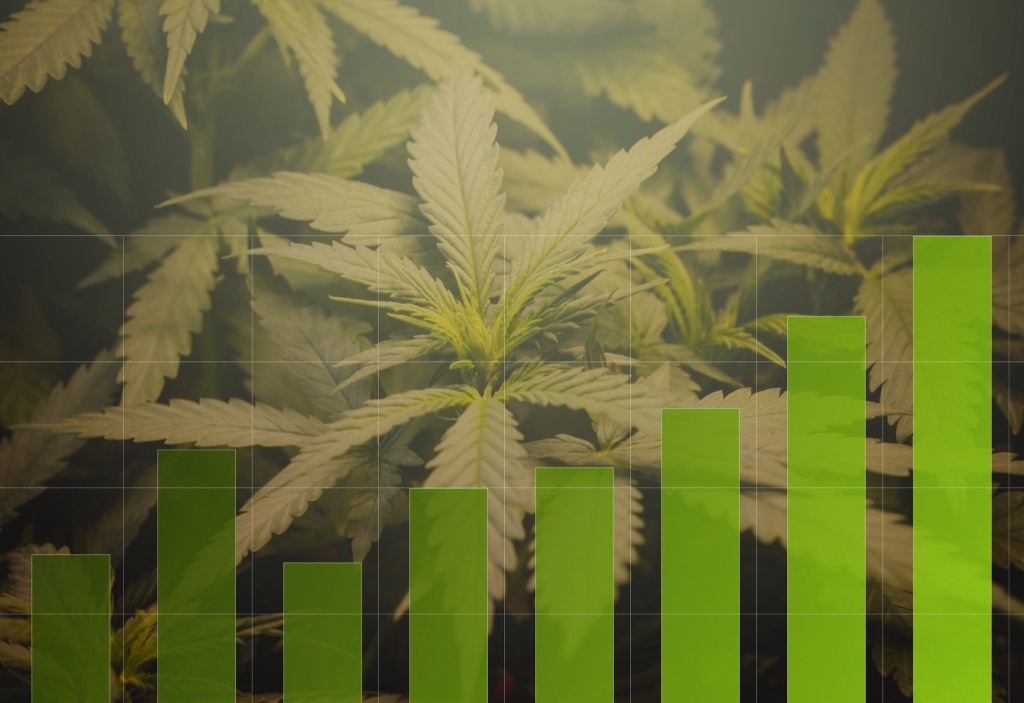
In cannabis manufacturing, especially within the booming pre-roll category, there’s no shortage of talk about speed and scale. Everyone wants to know how many joints per minute, how fast you can pack, and how much you can move. But the quieter metric—the one that can quietly drain margins or quietly drive profits—is uptime.
Downtime doesn’t just mean a machine is broken. It means labor costs continue while output stalls. It means the flower gets stale. It means packaging timelines are disrupted, orders are delayed, and your bottom line quietly erodes.
In this column, we’re pulling back the curtain on what downtime really costs cannabis processors and why uptime should be one of your top operational KPIs.
RELATED: Winning in hemp comes down to one thing
The Silent Margin Killer – Downtime You Didn’t Plan For
Downtime isn’t always dramatic. Sometimes the cause is operational—like not having the right people in place or running out of materials. Other times, it’s technical. It might look like your staff going on break while waiting on a part, or a shift losing 90 minutes to troubleshooting a cone jam. It might be a packaging delay because a supplier missed a shipment window.
Regardless of the cause, the impact is the same: your team is idle, your production line is stalled, and you’re still paying out wages. If you’re paying W2 labor and they can’t run because a machine is down or materials are missing, you’re not just losing time, but you’re also bleeding money.
Even minor interruptions add up fast. A single machine going down for 30 minutes per shift may not sound serious, but over the course of a month, that’s more than 10 hours of lost production. Multiply that by a dozen employees and the amount of product that didn’t move, and the labor cost becomes painfully clear.
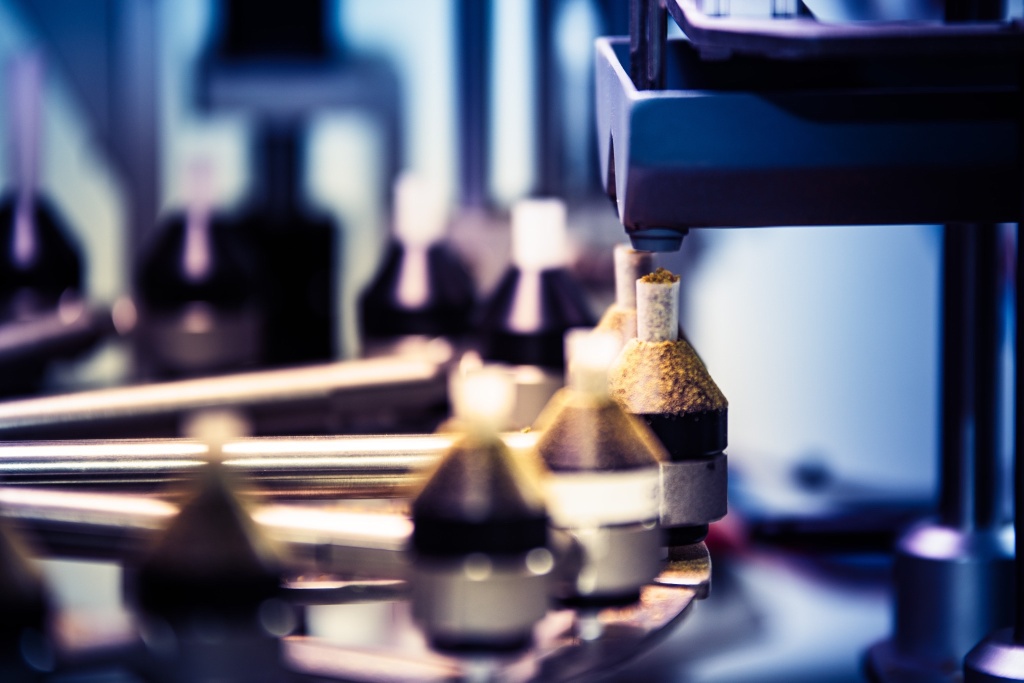
The Real ROI of Uptime: Planning Beyond the Machine
In high-volume cannabis manufacturing—especially in pre-rolls—every minute of uptime matters. We often talk about how fast a machine runs, but it’s also about how reliably it runs and how consistently you can keep the whole production environment moving. That starts long before flower hits the hopper.
Planning for uptime means taking a broad view of your supply chain and facility flow. Do you have enough flower on hand to meet demand? What happens if your cone or paper vendor misses a shipment? Can your team pivot if your product packaging gets delayed? Beyond a machine metric, uptime is a reflection of how resilient your operation is under pressure.
When production stalls due to missing packaging or raw materials, your automation is sitting idle, just like your people. You’ve invested in both, but you’re only getting a return when every element of the system is synced. This is why forward-thinking processors are putting more energy into supply chain redundancy, real-time production data, and equipment support partnerships that keep things moving.
RELATED: What rolling 100 million joints taught me about the cannabis industry
Build for Simplicity, Not Complexity
When choosing equipment, more features and moving parts don’t always mean better performance. In fact, over-engineered machinery is one of the biggest hidden risks to uptime. The more moving parts required to perform a single action, the more opportunities there are for failure, misalignment, or jams.
Think of it like directions to the beach—you can take many roads, but the most direct path is usually the most efficient. That same principle applies to cannabis automation. A machine that simplifies steps, uses straightforward mechanics, and eliminates unnecessary components will be easier to maintain and quicker to troubleshoot.
Leading manufacturers understand this and design equipment with uptime in mind from the start. That means intuitive layouts, easy-access components for cleaning and repairs, and a commitment to reducing friction points in daily operation. For example, using pneumatic components instead of complex electronic systems can cut down on required maintenance, eliminate oil changes, and streamline upkeep. These design choices matter, and they directly impact how much production time you actually get out of your investment.
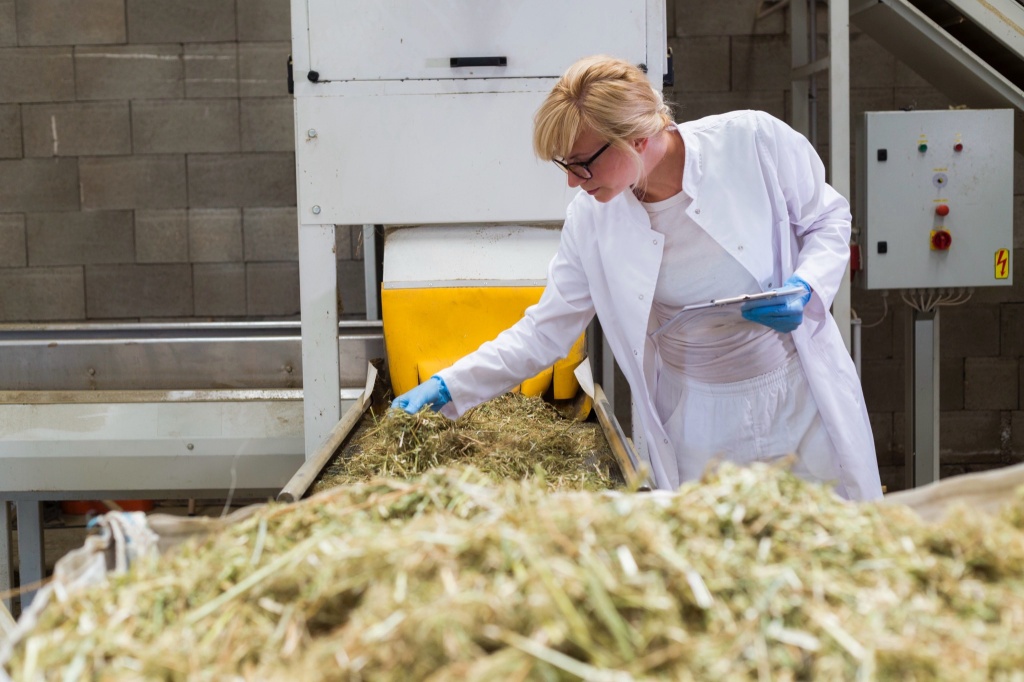
Preventative Maintenance Is 90 Percent of Uptime
A major differentiator between high-performing facilities and constantly stalled ones is the discipline of preventative maintenance. Fortunately, it doesn’t have to be complicated. In fact, with the right equipment, the majority of uptime preservation comes down to one thing: consistent cleaning and basic checks.
Easy access to the internal mechanics of your equipment (without needing a toolbox or specialist) means operators can stay ahead of common issues. Daily cleaning, regular alignment checks, and timely replacement of consumable parts are often all it takes to keep a production line humming. But this only works when the machine is designed with the operator in mind.
RELATED: Everyone working in weed should know this
Remote Support Should Be Built In, Not an Add-On
In today’s tech-driven world, remote machine access is an operational lifeline. Top-tier automation providers build in smart diagnostic tools that allow technicians to connect to your equipment remotely, assess the situation, and walk your team through real-time fixes.
The vast majority of service calls can be resolved by tweaking parameters or guiding operators through simple adjustments. When the alternative is flying in a tech or waiting days for onsite support, remote access becomes a critical factor in uptime. Especially in the cannabis space, where production windows are tight and delivery expectations are high, every hour saved makes a difference.
Choosing a vendor who shows up, answers the phone, and helps you get back online quickly is critical. That trust can only be earned through reliability.
Operational Culture Determines Uptime Outcomes
While technical simplicity and support are key, the companies that truly maximize uptime are also the ones that embed it into their operational culture. That means scheduling multiple shifts to fully utilize equipment, training staff to recognize and prevent slowdowns, and constantly refining SOPs to remove bottlenecks.
At Hefestus, we come from high-demand industries like food and beverage, so we understand this well. When shelf space is at risk and competitors are waiting to fill your order slot, downtime doesn’t just cost you dollars in the short-run but it’s actually existential. This mindset applies just as much to cannabis. The demand is there. The margins are tight. And the pressure to deliver fresh, compliant product at scale is only growing.
To keep up, processors need to make sure their equipment works for them, not the other way around. That means running two or even three shifts a day when demand calls for it, avoiding wasteful lulls between runs, and making full use of every dollar spent on rent, labor, and automation.
RELATED: Weed fans say only one thing matters when shopping at the dispensary
How to Choose the Right Equipment (and Vendor)
When evaluating new pre-roll equipment (or any automation), the focus should go far beyond speed specs or flashy features. Instead, ask the questions that get to the heart of long-term performance and support:
- What’s likely to break first, and how hard is it to replace?
- How many moving parts are there per key action?
- How easy is the machine to clean, access, and tune?
- Is remote support built in?
- Do they include a spare parts kit with critical components?
- Can I call their current customers and ask about their experience?
- Do they have boots-on-the-ground support in my region?
If a vendor can’t confidently walk you through all of this, or if their demo only includes salespeople and not engineers, that’s a red flag. That’s because in addition to buying a piece of equipment, you’re investing in a production partner. My biggest piece of advice is to call the automation provider’s current customers to get direct validation before making the investment.
Cannabis Processors: Make Uptime Your Next KPI
In cannabis, the race for scale often overshadows the importance of stability. But uptime is a make-or-break metric that impacts every corner of your operation. From labor utilization and inventory flow to order fulfillment and product freshness, every hour of consistent performance drives ROI.
Automation is a smart move—but only if it’s backed by simplicity, preventative care, and human support. When your machines are built to run, your team is trained to maintain, and your vendors are there when you need them, you’re not only minimizing downtime but also building a business that lasts.
*This article was submitted by a guest contributor. The author is solely responsible for the content.